給紡織工業(yè)穿上“環(huán)保內(nèi)衣”
時(shí)間:2016-08-22 來(lái)源: 瀏覽:
次
作為國(guó)內(nèi)傳統(tǒng)型產(chǎn)業(yè)支柱之一,傳統(tǒng)紡織行業(yè)因污染大、能耗高、耗水量大,一直是污染大戶。當(dāng)前,國(guó)內(nèi)部分大型紡織工廠在越來(lái)越高的環(huán)保壓力下被迫停產(chǎn)。脫不掉高能耗、高污染的外衣,傳統(tǒng)紡織行業(yè)將難以為繼。如何讓紡織工業(yè)成為低能耗、低污染的綠色工業(yè),是急需解決的難題。
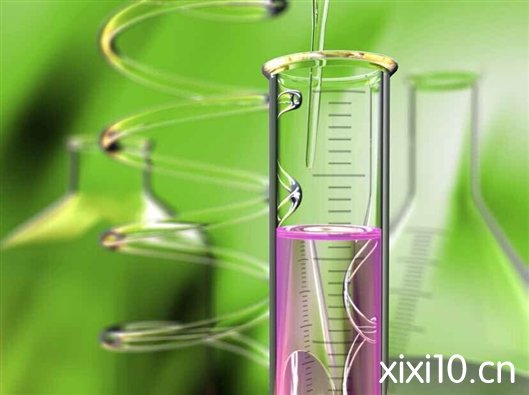
不久前,中國(guó)科學(xué)院天津工業(yè)生物技術(shù)研究所開(kāi)發(fā)了生物酶法綠色染前處理工藝,并在河北寧紡集團(tuán)成功完成10萬(wàn)米布的生物酶法前處理工藝的應(yīng)用示范和推廣,為該難題開(kāi)出了藥方。傳統(tǒng)的染前處理工藝流程包括燒毛、退漿、精煉、漂白和絲光等5個(gè)步驟。在這一過(guò)程中,必須用大量的燒堿和助劑等化學(xué)制劑,耗費(fèi)大量的水和能源,造成嚴(yán)重的環(huán)境污染。據(jù)統(tǒng)計(jì),目前我國(guó)單位織物能耗為世界平均水平的2.4倍;以棉織物為例,1萬(wàn)米棉織物處理需300噸水。與此同時(shí),纖維易損傷,設(shè)備易損壞。
針對(duì)這一現(xiàn)狀,中科院天津工業(yè)生物技術(shù)研究所與天津天紡集團(tuán)、河北紡聯(lián)物資供銷(xiāo)有限公司開(kāi)展合作攻關(guān),歷經(jīng)三年,研發(fā)出多種性質(zhì)優(yōu)良的紡織用生物酶制劑及生產(chǎn)工藝。他們自主研發(fā)的復(fù)合酶制劑,可以將傳統(tǒng)工藝中的退漿和精煉合并成一步完成,從而大大提高了前處理效率。
據(jù)介紹,酶法退漿精煉一浴完成,降低了蒸汽能耗、省去堿性廢水處理成本、減少多種化學(xué)助劑用量,可顯著降低前處理成本、提高紡織行業(yè)的經(jīng)濟(jì)效益。實(shí)踐證明,與傳統(tǒng)堿法工藝相比,用酶法前處理工藝生產(chǎn)12000米純棉棉布和11000米芳綸熱波卡布,成本可分別降低30%和70%。
值得一提的是,生物復(fù)合酶制劑還具有處理?xiàng)l件溫和、效率高、專一性好等特點(diǎn),不僅對(duì)棉纖維幾乎沒(méi)有損傷,還能提高產(chǎn)品品質(zhì)。